Одной из основных задач внедрения ERP-систем на промышленных предприятиях является производственное планирование. Для успешного решения этой задачи ERP-система должна оперировать определенным объемом нормативно-справочной информации, без которой планирование либо будет неэффективным, либо не сможет осуществляться вовсе.
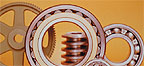
Эта информация нередко создается и хранится в системах управления данными об изделии — PDM-системах. Таким образом, становится необходимым обеспечить обмен данными между системами классов ERP и PDM.
Задачи интеграции
Информацию об изделии условно можно разделить на два больших блока: данные, связанные с конструкторско-технологической подготовкой производства, и данные, связанные с управлением материальными потоками. Для решения задач управления материальными потоками используются входящие в любую ERP-систему модули логистического контура («Управление закупками», «Управление запасами», «Заказы», «Закупки», «Склад» и т. д.). Их возможностей, как правило, достаточно для того, чтобы полностью удовлетворить потребности предприятия в управлении движением материалов, их закупкой и хранением.
Основой данных для подготовки производства является конструкция изделия. На этапе конструирования не только формируется концептуальный облик будущего изделия, но и создаются математически точные геометрические модели как всего изделия в целом, так и отдельных его деталей. На этом же этапе создаются спецификации — по сути, описание состава изделия, нормы расхода материалов, необходимых для производства и т. д. Разработка конструкции изделия выполняется с помощью пакетов автоматизированного проектирования — CAD-систем.
В силу особенностей задач, решаемых отдельными конструкторами и технологами, на предприятиях используется множество строго специализированных пакетов. Например, для создания объемных моделей изделий машиностроения можно использовать методы твердотельного либо поверхностного моделирования (и соответствующие CAD-системы). Для разработки большинства деталей и узлов машиностроительных изделий достаточно использовать твердотельное моделирование, однако некоторые задачи, например проектирование сложных изделий, изготовляемых штамповкой, или внешних поверхностей деталей для самолетов, автомобилей, бытовой техники, могут быть выполнены только с использованием поверхностного моделирования. Нередко предприятию приходится решать и другие задачи, связанные с разработкой, например проектировать разводку для печатных плат (если в изделие входят электронные компоненты), выполнять инженерный анализ конструкции и т. д. Эти задачи также решаются с помощью соответствующих CAD-систем.
Итак, возникает первая проблема — интеграции различных CAD-систем предприятия между собой. Рассмотрение этой проблемы выходит за рамки данной статьи. Скажем только, что проблема эта достаточно сложная и полностью решить ее пока не удалось.
Второй важной составляющей для формирования нормативной базы, необходимой для производственного планирования, является технологическая подготовка производства. Задачи разработки технологических маршрутов решаются с помощью специализированных систем автоматизированного проектирования техпроцессов. Для разработки управляющих программ для станков с ЧПУ и расчета режимов резания также используются специализированные программные пакеты.
Следовательно, возникает вторая проблема — интеграции САПР подготовки техпроцессов и специализированных технологических систем.
Еще одна проблема, связанная с разработкой конструкции и технологии производства, касается синхронизации данных об изделии и налаживании документооборота. Согласно статистике, на один конструкторский документ, например лист чертежа формата А4, может приходиться до 15 листов технологической документации. В случае изменения конструкции или технологии изготовления выпускаются извещения об изменении, разрешения на замену материалов или на временное отступление от нормативной документации. На среднем машиностроительном предприятии количество таких извещений может доходить до 50 и более в день. Сейчас конструктор и технолог до 35% своего рабочего времени вынуждены тратить на поиск в архивах необходимой документации и ее обработку. Еще примерно 20% времени тратится на ожидание запрошенной документации, ее копирование, доставку и т. д. На крупных машиностроительных предприятиях, где изделие может состоять из тысячи и более компонентов, проблема стоит еще острее.
В то же время в современной высококонкурентной среде скорость разработки и вывода на рынок новых продуктов является одним из ключевых факторов успеха для предприятия.
Ответом производителей ПО на перечисленные выше проблемы стали появившиеся в начале 90-х системы управления данными об изделии — PDM-системы, которые являются, по сути, центром интегрированной системы управления, связующим звеном между всеми системами в корпоративной среде предприятия. Посредством PDM также решается задача интеграции различных CAD-систем и систем технологического проектирования. Одним из важнейших преимуществ использования PDM-системы является возможность формирования на предприятии непротиворечивой базы нормативно-справочной информации и поддержки ее в актуальном состоянии.
Мост между ERP и PDM
Ведущие поставщики ERP-систем в последнее время уделяют все большее внимание вопросам интеграции с PDM, так как это может обеспечить ERP-систему актуальной нормативной информацией для планирования и существенно сократить избыточность данных и затраты времени на передачу изделий из разработки в производство.
Для решения задачи интеграции ERP и PDM Международная организация по стандартам (ISO) в середине 90-х годов разработала набор стандартов ISO 10303 STEP, включающий в себя различные прикладные протоколы интеграции, язык разработки Express для описания моделей данных, механизмы тестирования и т. д. Был разработан целый ряд продуктов для технического обеспечения стандарта, получивших название STEP-средств, куда входили редакторы, компиляторы, конвертеры и т. д., связанные с языком Express. Поддержка этого стандарта производителями CAD-, ERP- и PDM-систем могла бы существенно облегчить проблемы интеграции приложений между собой. Однако, несмотря на все усилия, стандарт ISO не получил широкого распространения, и сегодня на рынке не так много систем, поддерживающих интеграцию с его помощью.
На Западе предпринимаются попытки использовать для интеграции становящиеся все более популярными в последнее время специализированные системы интеграции приложений предприятия (Enterprise Application Integration, EAI), такие, например, как Microsoft BizTalk и BEA WebLogic. Однако такие решения достаточно сложны, дороги и пока не получили широкого распространения.
В основном (по крайней мере, на известных мне предприятиях) интеграция выполняется двумя путями: либо с помощью API, либо с помощью файлов экспорта/импорта данных.
Использование API более вписывается в традиционные представления о технологической интеграции и позволяет добиться более тесной интеграции систем, однако имеет ряд ограничений. Прежде всего, существует сильная привязка разработанного интерфейса к конкретным версиям интегрируемых продуктов. Даже незначительные изменения в структуре данных одного из таких продуктов могут потребовать переработки интерфейсов. Кроме того, для разработки интерфейсов необходимы достаточно серьезные знания в программировании.
Использование файлов экспорта/импорта для интеграции, хотя и менее технологично (обмен файлами в разы проще, чем применение других средств интеграции), тем не менее в ряде случаев обеспечивает более гибкий подход и не требует столь глубоких знаний в программировании, как при использовании API. Наверное, поэтому большинство проектов по интеграции выполняется именно таким способом.
Возможный вариант
Для иллюстрации подхода к интеграции с использованием файлового обмена рассмотрим модуль интеграции ERP- и PDM-систем, разработанный компаниями «АНД Проджект» и «Аскон» в рамках реализации проекта построения комплексной системы управления на одном из крупных российских машиностроительных предприятий — ОАО «Техприбор». В качестве PDM-системы на предприятии была выбрана система PartY PLUS, которая интегрирована с приложениями для конструкторской и технологической подготовки производства — CAD-системами «Компас 3D» и «Компас График», в которых ведется основная работа по разработке конструкции изделий, системой проектирования технологических процессов «Компас Автопроект» и системой подготовки управляющих программ для станков с ЧПУ «Гемма 3D».
Кроме того, на предприятии активно используются системы AutoCad 2000, служащая для оформления чертежей, Simatron для проектирования оснастки и подготовки управляющих программ для станков с ЧПУ, PCAD 2000 для проектирования печатных плат и т. д. Все эти продукты также полностью интегрированы с PDM-системой.
В качестве ERP-системы предприятие использует систему Microsoft Business Solutions-Axapta, поставщиком которой стала компания «АНД Проджект».
Для интеграции двух систем специалистами «АНД Проджект» и «Аскон» был разработан специальный модуль, который обеспечивает передачу нормативно-справочной информации из PDM-системы PartY PLUS в ERP-систему. Передача данных осуществляется с помощью файлов импорта/экспорта. Набор данных, которыми оперирует система PartY PLUS, существенно больше, чем тот, который необходим ERP-системе для реализации функций планирования и управления производством: ERP-системе нужны только состав изделия, нормы расхода материалов, технологические маршруты с перечнем операций и рабочих центров и времена их выполнения. Все остальные данные PDM являются для ERP-системы излишними.
Схема взаимодействия систем выглядит следующим образом. Из PDM-системы PartY PLUS автоматически в реальном времени извлекаются необходимые данные (номенклатурные единицы, версии спецификаций, состав спецификаций, технологические операции, рабочие центры, версии маршрутов, маршруты). Данные, получаемые в виде файлов экспорта, с помощью модуля интеграции преобразуются в формат, понимаемый ERP-системой Axapta, при этом происходит удаление излишней информации, и затем импортируются в ERP-систему.
В свою очередь, из ERP-системы в PDM передаются справочники материалов, оборудования, единиц измерения (механизм обмена информацией аналогичен описанному выше). Этот обмен необходим для синхронизации данных в системах.
Кроме передачи нормативных данных о новых изделиях модуль интеграции обеспечивает обработку извещений (событий), что также необходимо для синхронизации данных об изделии. Как только конструктор или технолог регистрирует в PDM-системе извещение об изменении состава изделия, изменении технологического маршрута и т. д., оно немедленно обрабатывается, и в ERP-систему передаются новые версии спецификаций и технологических маршрутов. Обмен данными происходит в режиме, близком к реальному времени. Например, от момента появления извещения в PDM-системе до передачи его в ERP-систему Axapta проходит менее минуты. Реализация этого механизма стала возможна во многом благодаря мощным функциям управления версиями спецификаций и маршрутов, реализованным в системе Axapta.
Необходимо отметить, что работы по внедрению PDM-системы PartY PLUS и ERP-системы Microsoft Business Solutions-Axapta с самого начала планировались и выполнялись одновременно, в рамках единого проекта по созданию комплексной системы управления. Специалисты компаний, внедрявших системы, совместно с сотрудниками завода провели огромную работу по выверке нормативной базы предприятия, формированию справочников и архивов в PDM-системе, изменению существующих бизнес-процессов в части ведения нормативной базы предприятия. Разработанное интеграционное решение уже больше года находится в промышленной эксплуатации.
Использование модуля интеграции позволяет создать на предприятии единую информационную среду, обеспечивающую реализацию концепции CALS (Continuous Acquisition and Life Cycle Support — непрерывность поставок и поддержки жизненного цикла продукции), т. е. дает предприятию возможность управлять замкнутым производственным циклом, включающим в себя подготовку производства, его планирование и оперативное управление.
Аркадий Черняков — директор по развитию компании «АНД Проджект», achernyakov@andproject.ru
Следует подходить индивидуально

Виктор Исправников, начальник АСУ ОАО «Техприбор» (на этом предприятии реализована схема интеграции систем ERP и PDM посредством файлов), подтвердил, что обмен данными между Microsoft Business Solutions-Axapta и PartY PLUS осуществляется в реальном времени. Интеграция достигается благодаря синхронизации изменений данных, которыми обмениваются системы: информация о факте модификации данных в одной из систем передается в модуль интеграции, который, в свою очередь, инициирует в другой системе выборочную загрузку данных из файла, используемого в качестве буфера обмена. Особых проблем с такой схемой не возникает, правда, при первичной загрузке данных наблюдаются проблемы, связанные со снижением производительности приложений. «Интеграция создает дополнительную нагрузку на системы», — заметил Исправников. С появлением новых задач, затрагивающих обмен данными между системами, механизмы интеграции приходится совершенствовать.
Оценивая возможность применения этого способа интеграции на других предприятиях, Исправников рекомендует взвешенно подходить к вопросам стыковки разнородных систем, исходя из особенностей конкретного предприятия и возможностей систем, которые необходимо стыковать между собой.
— ДИС